
Rubber Components
The Rubber Group is a recognized industry leader in compression molding, specializing in the production of durable, high-performance rubber components designed to meet the most demanding specifications across various industries.
The Rubber Group is a leader in compression molding, producing precisionengineered rubber components with exceptional consistency, durability, and reliability. This process allows for the creation of complex, high-performance parts ideal for industries such as automotive, aerospace, medical, and industrial equipment. By refining mold design and processing techniques, the company
ensures minimal waste, high efficiency, and superior mechanical properties. Our expert engineering team collaborates with clients to select the best elastomer compounds—EPDM, silicone, natural rubber, or specialty formulations—while offering secondary services like trimming, bonding, and post-curing.
With advanced molding capabilities and deep technical expertise, The Rubber Group delivers cost effective, high-quality rubber solutions tailored to demanding applications.
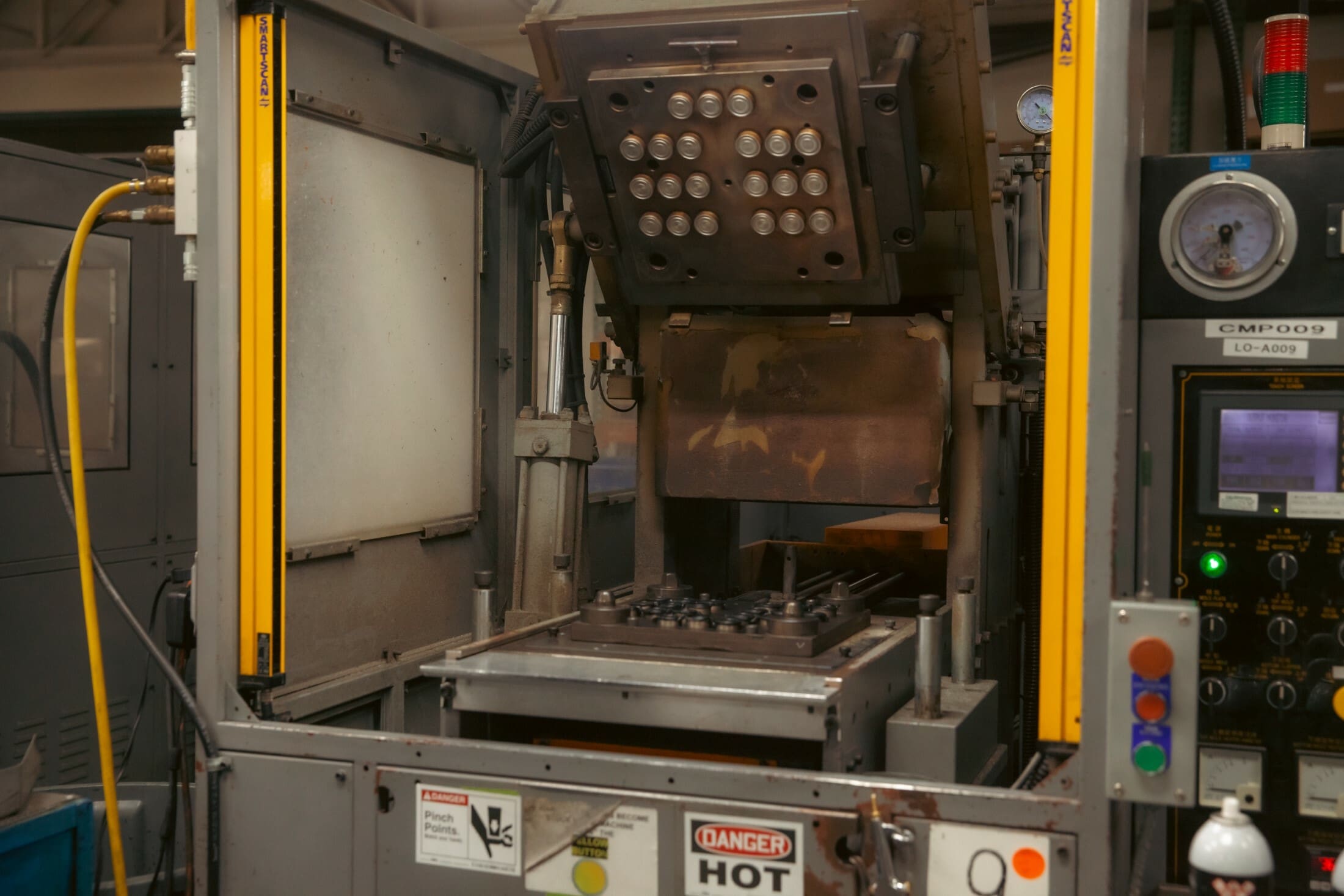
Pros (Ideal for):
- Large and heavy-duty rubber components
- Smaller parts requiring superior mechanical performance
- Complex external geometries
- Components with tight tolerance requirements
- Rubber parts requiring exceptional durability
- Consistent performance characteristics
Specific Industry Applications:
- Aerospace critical sealing elements
- Medical device precision parts
- Industrial equipment robust components
- Oil-resistant seals
- High-temperature gaskets
- Vibration isolation mounts
- Custom-engineered specialized parts
Limitations
- Higher per-unit Costs for Large Production Runs
- More Labor-Intensive than Automated Molding
- Techniques
- Requires Precise Material Pre-Measurement
- Higher Material Waste Potential
- Less Suitable for Complex Multi-Cavity Designs
- Not ideal for extremely thin or intricate internal geometries
Decision Factors / Comparative Manufacturing:
- Better alternative for high-volume production: Injection molding
- Better for complex internal structures: Transfer molding
- More cost-effective for thin parts: Injection molding